Tin boxes are popular packaging materials for their durability, versatility, and aesthetic appeal. But have you ever wondered how these boxes are made?
In this article, we’ll explore the manufacturing process of tin boxes and answer some common questions about their materials, uses, and sustainability.
Main Raw Materials of Tin Box
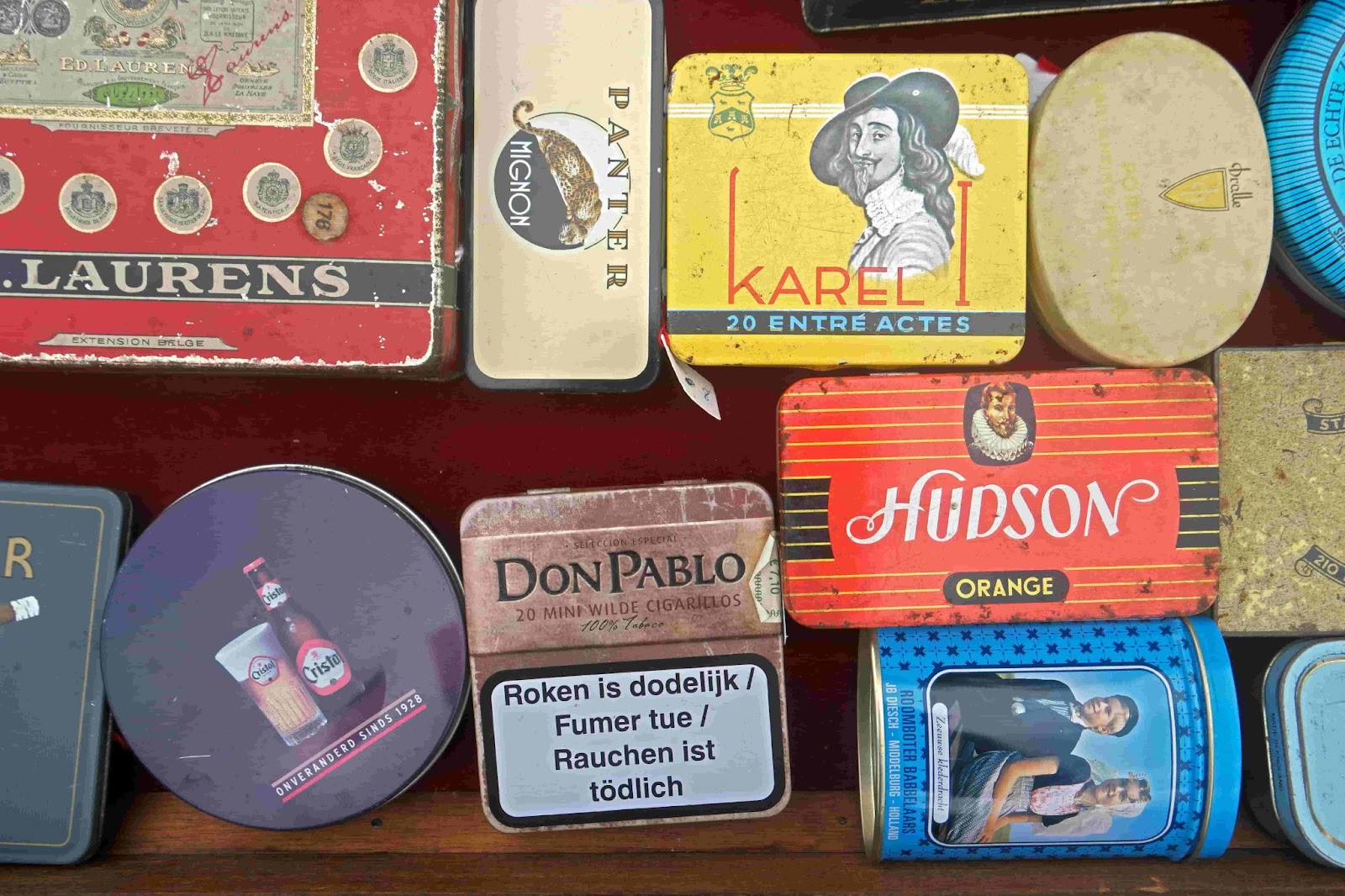
Tin boxes are made from a combination of metals, primarily steel and a thin layer of tin. The process involves coating a steel sheet with a layer of tin, which gives the box its shiny, corrosion-resistant properties. Here’s a breakdown of the materials used:
Steel Core
The base material for most tin boxes is steel. Steel is strong, durable, and cost-effective, making it an ideal choice for the structure of the box.
Tin Coating
Tin is a soft, corrosion-resistant metal that is applied as a thin layer over steel. This process, known as tin plating, gives the box its characteristic appearance and protects it from rust.
Other Materials
In some cases, manufacturers may add other materials like aluminum or specialized coatings for enhanced functionality, such as water resistance or anti-corrosion properties.
The combination of steel and tin ensures that tin boxes are both lightweight and durable, able to withstand everyday handling while maintaining their aesthetic appeal.
What Are Tin Boxes Usually Used For?
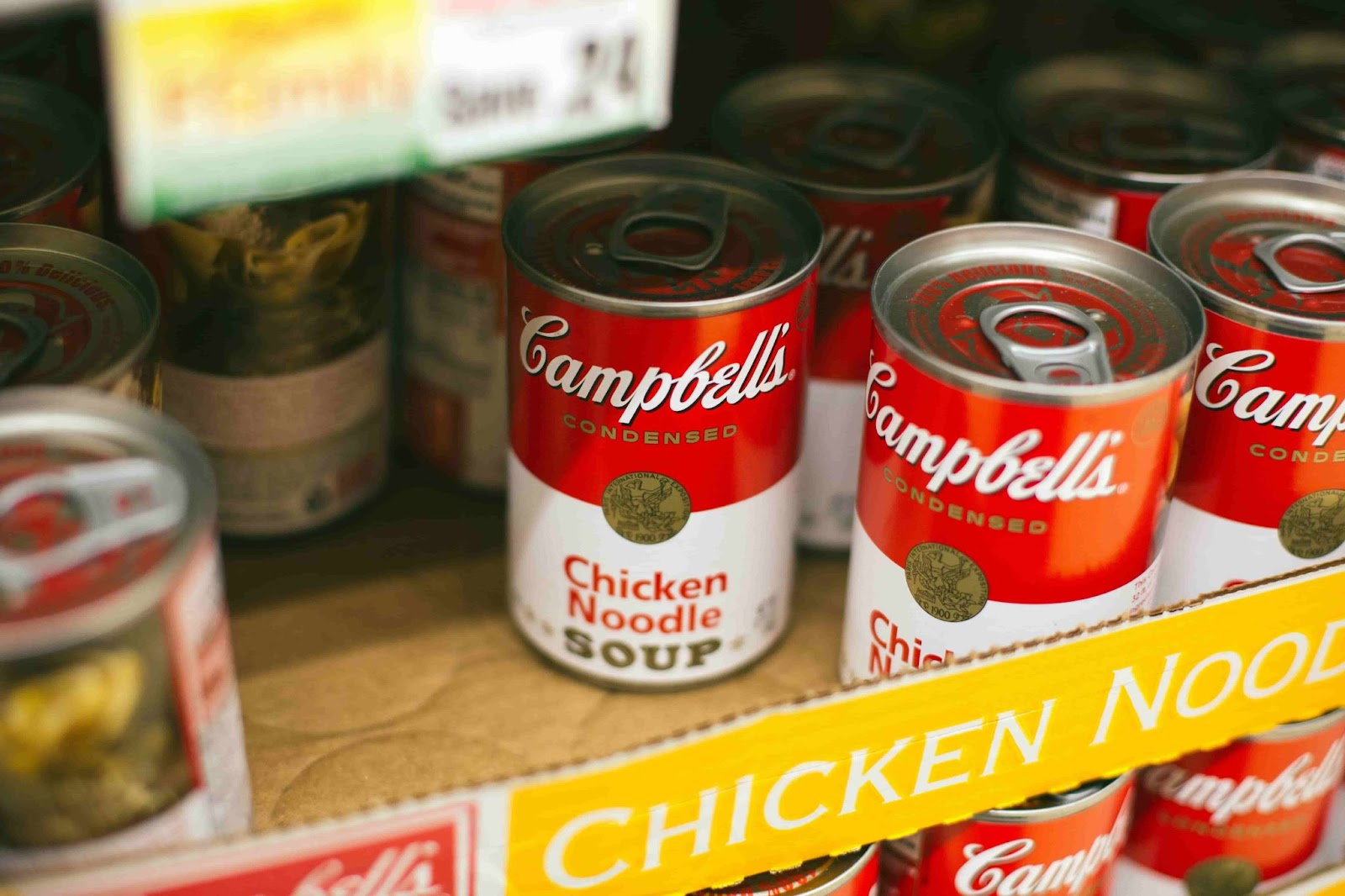
Tin boxes have a wide range of applications across various industries due to their sturdy construction and attractive appearance. Here are some of the most common uses:
Packaging for Food Products
Tin boxes are often used to package food items like cookies, chocolates, and teas. Their airtight seal helps to preserve freshness and protect the contents from contamination. At the same time, you can also customize tin boxes of various shapes and uses.
Gift Boxes and Promotional Packaging
Due to their visual appeal, tin boxes are frequently used for packaging gifts, collectibles, and promotional items. They can be easily customized with logos, colors, and designs to suit the branding of a business. A custom tin box can be an excellent way for businesses to enhance their marketing efforts and create a unique product offering.
Storage Containers
Beyond packaging, tin boxes are also used for storage purposes. Their durability makes them ideal for holding small items, such as jewelry, office supplies, or even keepsakes.
Candle Packaging
Tin boxes are often used to package candles. The boxes are designed to be both functional and aesthetically pleasing, offering an attractive and safe way to store candles.
These boxes are highly versatile, and their applications span across industries such as food and beverage, retail, cosmetics, and even home decor.
The Tin Box Manufacturing Process
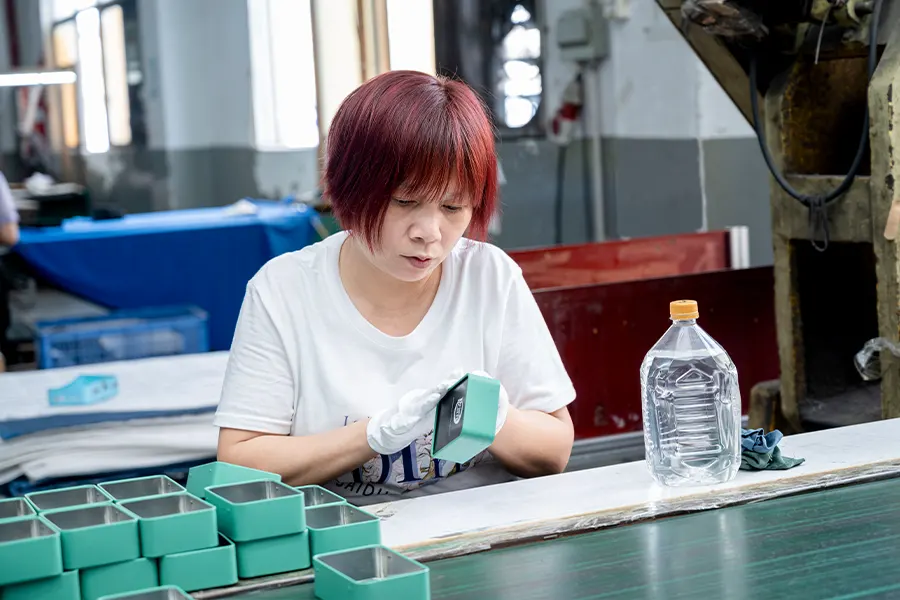
Now that we understand what tin boxes are made of and the key uses and applications for them, let’s dive deeper into the process of manufacturing a tin box. This step is essential for producing a high-quality tin box.
Material Selection and Preparation
The process begins with selecting high-quality steel sheets, which are then cleaned to remove any oils or debris. The steel is coated with a layer of tin through a process called electroplating.
Cutting and Shaping
Once the material is prepared, it is cut into the desired shapes using die-cutting or laser-cutting techniques. The pieces are then formed into the box’s structure through stamping or pressing.
Printing and Decoration
After the box has been shaped, it’s time for decoration. Printing processes such as lithographic printing are used to add designs, logos, or text to the box. This step ensures that the final product is visually appealing and ready for branding.
For businesses seeking unique packaging solutions, working with a tin box manufacturer can help create custom tin box designs that align with branding requirements.
Assembly
The parts of the box, such as the lid and base, are assembled using techniques like welding, folding, or gluing. The box is then tested for durability and functionality.
Quality Control and Packaging
Before the tin boxes are shipped to customers, they undergo rigorous quality control checks to ensure that they meet industry standards. Once approved, they are packed and ready to be sent out for use in a wide range of applications.
Shipping
After packaging the products, send the finished products to customers on time.
Quality Control Steps
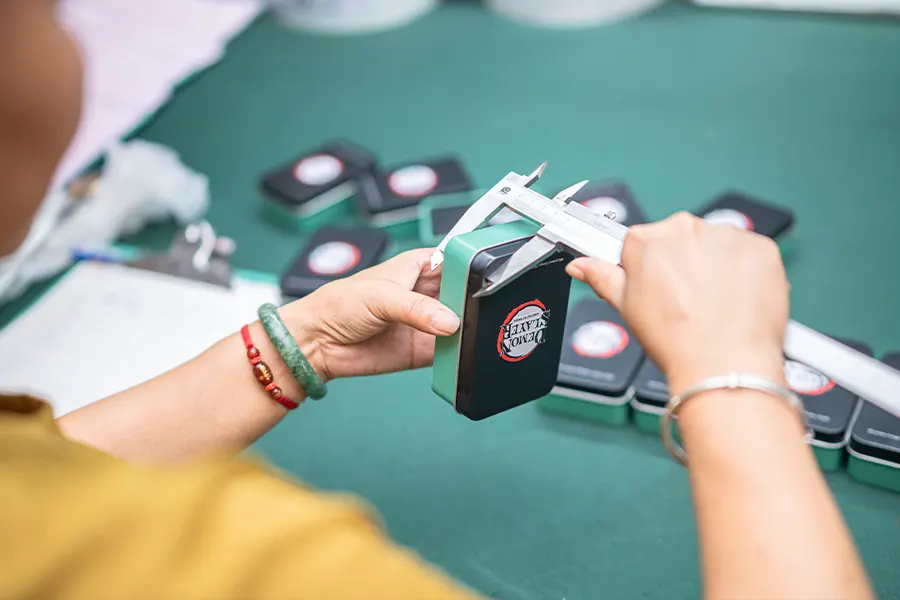
Our state-of-the-art R&D facilities include advanced 3D modeling software, 3D printers, and automated production lines. This technological edge allows us to handle complex designs with precision and efficiency.
In-Process Quality Assurance
- Real-Time Checks
Ongoing inspections during production to identify and address issues immediately.
- Defect Removal
Immediate removal of scratched, uneven, or deformed products.
- Mold Adjustments
Timely mold adjustments to prevent defects and ensure consistent production.
- Skilled Workforce
Our experienced workers are dedicated to maintaining product excellence at every step.
Product Quality Testing
- Certified by third-party testing agencies
To further assure our clients, we offer third-party quality inspections before shipment. We collaborate with professional inspectors chosen by our clients to examine our products thoroughly.
Only after these inspectors approve the quality of our tins do we proceed with shipping. This additional layer of scrutiny ensures that our clients receive products that meet their exact specifications and expectations.
- Detail Documentation
Detailed documentation of all quality checks and tests to ensure traceability.
About Tinmen
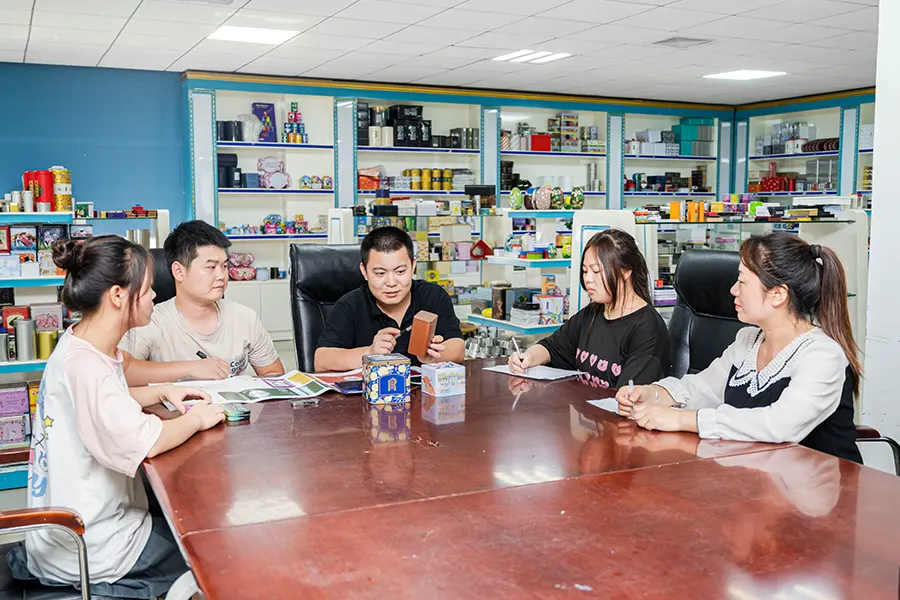
With over 30 years of industry experience, we specialize in producing high-quality tin cans for various applications. Our commitment to innovation, quality, and customer satisfaction sets us apart as a trusted partner in the tin packaging industry.
In terms of variety, we have many different shapes of tin boxes, square, round, etc. If you need to use it to hold food, we also have special biscuit boxes, tea boxes, cake boxes and so on.
Our products are certified by SEDEX, Disneyland, SIRA, and SGS, ensuring the highest quality standards. Let’s achieve success together!
FAQs
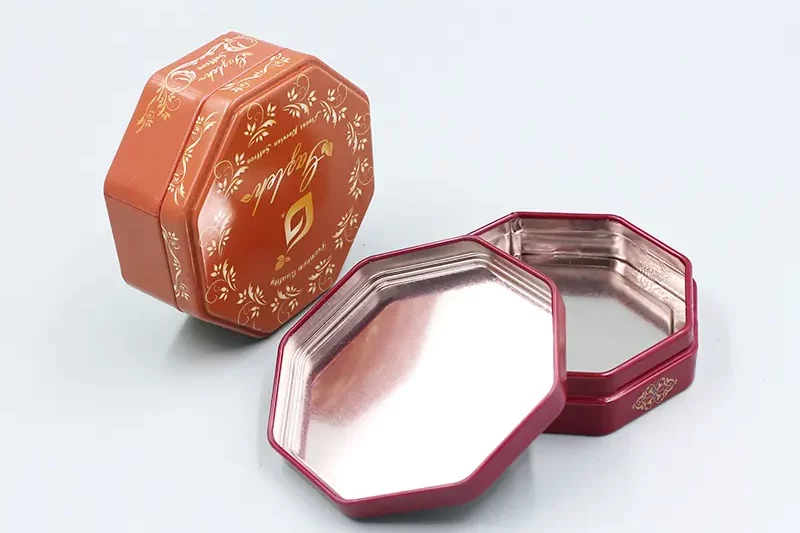
Are tin containers better than plastic?
Depending on the application and cost, metal cans offer advantages in certain areas, while plastic bottles continue to be a popular choice for some products. However, from an environmental perspective, metal cans, particularly aluminum, are a more sustainable option compared to plastic containers.
Are tin boxes recyclable?
Yes, tin boxes are recyclable! Not only that, tin boxes are safe and you can buy them with confidence. Their composition, primarily steel with a thin layer of tin plating, makes them highly recyclable. Since steel is a widely recyclable material, tin boxes are an eco-friendly packaging choice.
Recycling tin boxes not only helps reduce waste but also conserves valuable resources, making them a more sustainable alternative to many other packaging materials.
What are the disadvantages of tin boxes?
Tin boxes are relatively heavy, which can increase transportation costs. They also tend to take up more space compared to other packaging materials. Additionally, tin boxes are susceptible to rusting if the tin coating is damaged or scratched.
In addition, the advanced manufacturing needed for metal tin containers is not eco-friendly. The requirement to mine the ore and smelt the metal causes significant pollution.
What is the difference between a can and a tin?
Some people suggested that tin was a British word originating from the material the container is made from, while can is a US word for a sealed metal container with all the air removed. More suggested that tin should be used for food and can for drink, while some said that the correct expression was ‘tin can’.
Conclusion
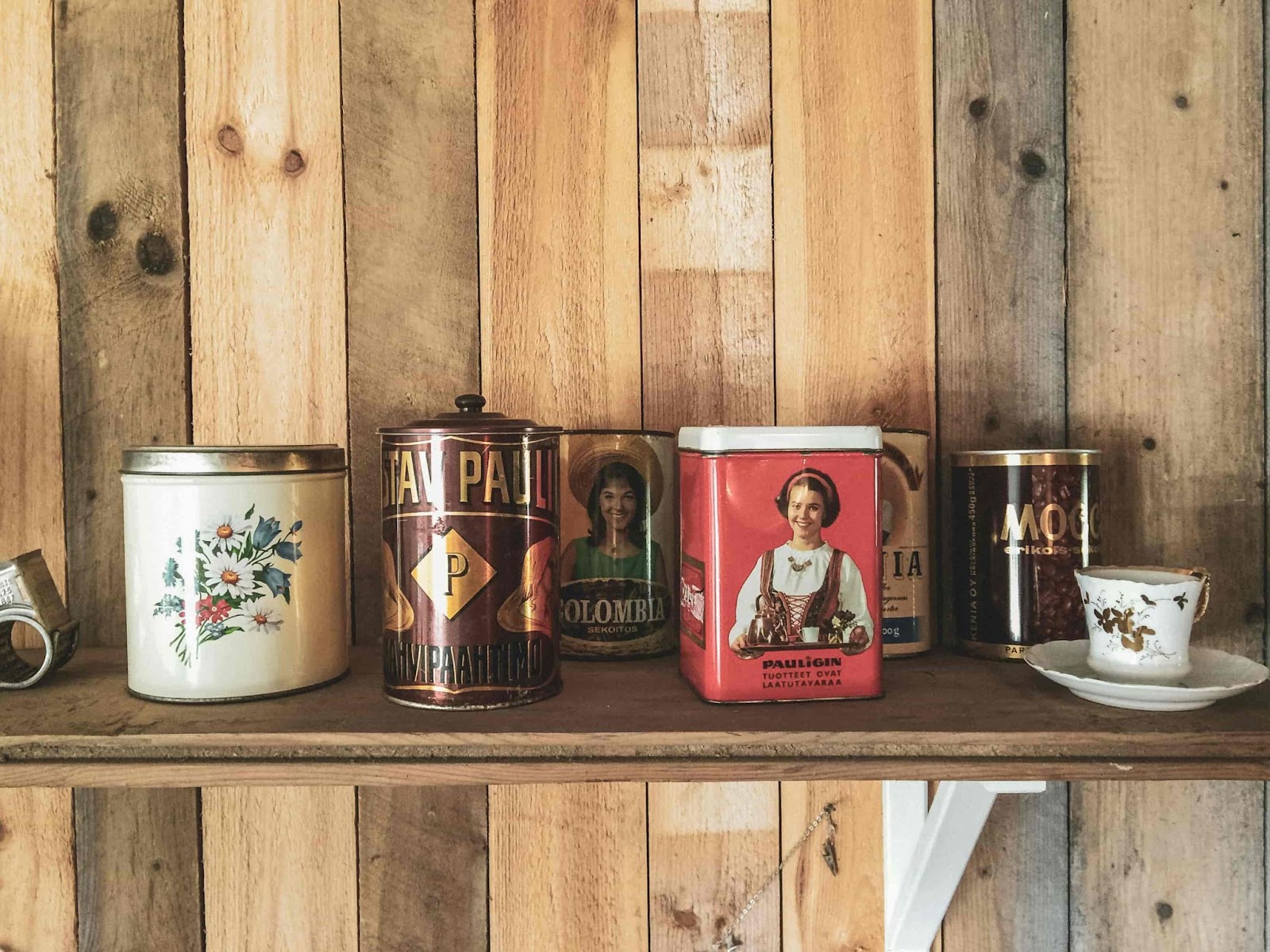
The manufacturing process of tin boxes combines advanced technology and high-quality materials to create a product that is not only visually appealing but also durable. Whether used for packaging food products, promotional items, or as a stylish storage solution, tin boxes offer a wide range of benefits.
By working with a reliable tin box manufacturer, companies can create custom tin boxes that meet their specific needs and enhance their branding efforts, all while ensuring that their products are made with sustainability in mind.